A three-interface random pore model: the reduction of iron oxide in chemical looping and green steel technologies
PROCEEDINGS OF THE ROYAL SOCIETY A-MATHEMATICAL PHYSICAL AND ENGINEERING SCIENCES(2023)
摘要
Accurate modelling of the gaseous reduction of porous iron oxide powders or fines is important in industry for (i) reinventing the carbon intensive production of iron and steel and (ii) chemical looping technologies in the sphere of carbon capture and storage. A new three-interface random pore model is derived and applied to the gaseous reduction of hematite (Fe2O3) to iron (Fe). The structural reaction-diffusion model is able to describe three simultaneously reacting oxide layers, Fe2O3, magnetite (Fe3O4) and wustite (FewO). The geometric nature of the model encodes structural information about the particles (porosity, surface area, pore length and size distribution), measured here by experiment. The model is usefully able to separate structural particle properties from individual rates of reaction and product layer diffusion. The results have been compared and fitted to thermogravimetric experiments between 800-1000 degrees C and three CO/CO2 gas mixtures. Rate constants for each indvidual reaction have been obtained and fit well to Arrhenius plots. The reduction of Fe2O3-Fe3O4 was controlled by diffusion and reaction kinetics, while the reduction of Fe3O4-FewO and FewO-Fe was limited by reaction kinetics. Metallization rates of the iron oxide powders were rapid, showing promise for both hydrogen-based direct reduced iron and chemical looping processes.
更多查看译文
关键词
random pore model,chemical looping,iron oxide reduction
AI 理解论文
溯源树
样例
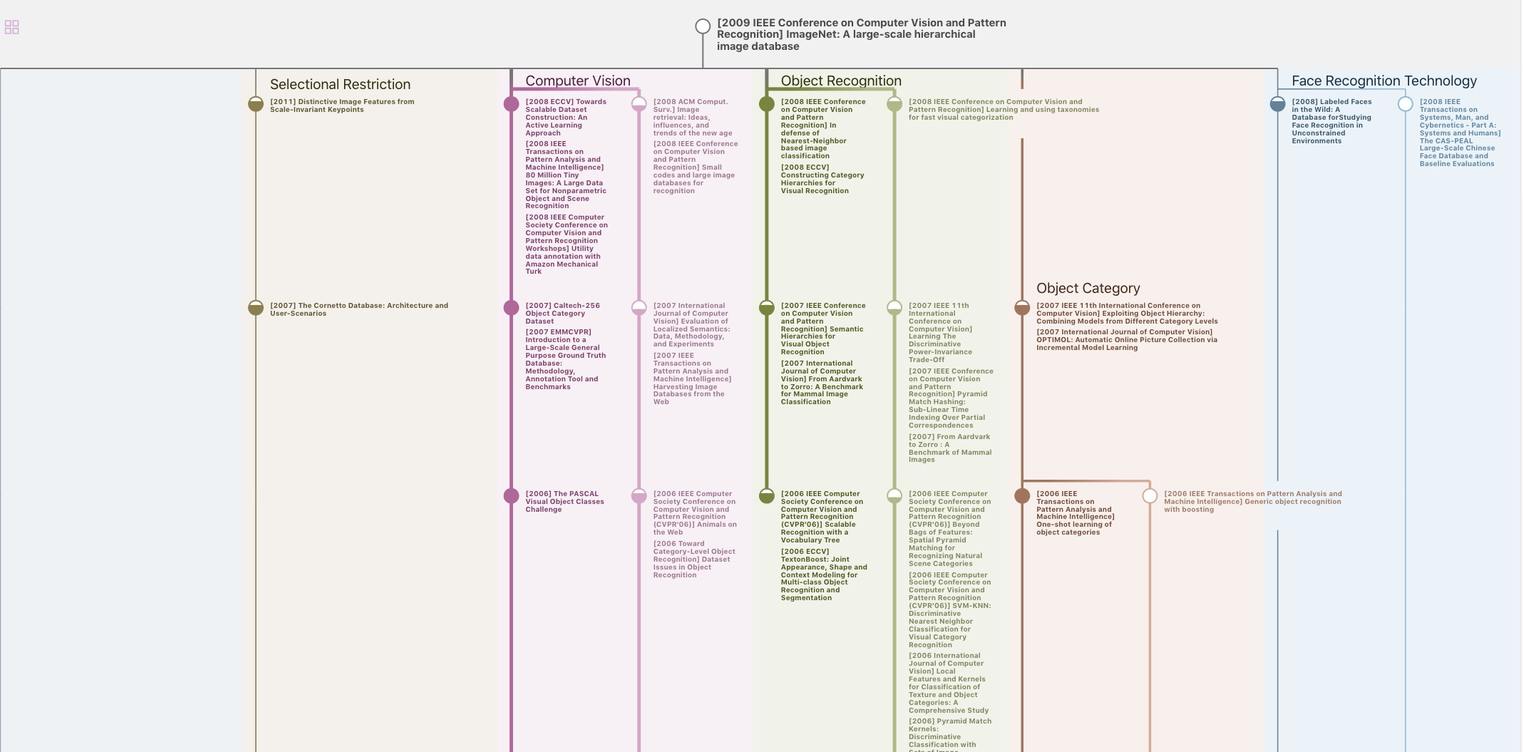
生成溯源树,研究论文发展脉络
Chat Paper
正在生成论文摘要