Rigid Mode Vibration Control for 250 HP Air Compressor System with Integrated Hybrid Air-Foil Magnetic Thrust Bearing(i-HFMTB)
Journal of engineering for gas turbines and power(2023)
摘要
Abstract This study aims to verify the effectiveness of the 250 HP class compressor system to which the integrated hybrid air foil magnetic thrust bearing (i-HFMTB) proposed in part I is applied, and the vibration and instability problems of air foil journal bearing (AFJB) occurring in the rigid mode are controlled by i-HFMTB. The compressor rotor is supported by two AFJB (journal diameter = 60mm) and an i-HFMTB, and the length and mass of the rotor are 550mm and 15.24kg, respectively. i-HFMTB has a structure in which air foil thrust bearing(AFTB) pads are inserted into eight slotted active magnetic thrust bearings (AMTB), and PD control (proportional gain: 4,000 /differential gain: 10) is applied. The operating area was identified through AFJB's dynamic coefficients and rotordynamic analysis. As a result with the experiment of the 250 HP compressor system supported only by two AFJB, sub- and super-synchronous vibrations were generated owing to the AFJB's insufficient load capacity and damping in the rigid mode (7,000rpm) region, and this instability did not disappear even upon increasing the speed to 15,000rpm. However, when i-HFMTB was turned on in rigid mode, it was confirmed that the sub- and super-synchronous vibrations were significantly reduced. The thrust collar tilt angle was calculated through orbit trajectory analysis of the impeller and cooling side, and it was confirmed that the tilt angle of the thrust collar was reduced during i-HFMTB operation.
更多查看译文
关键词
rigid mode vibration control,hp air compressor system,bearingi-hfmtb,air-foil
AI 理解论文
溯源树
样例
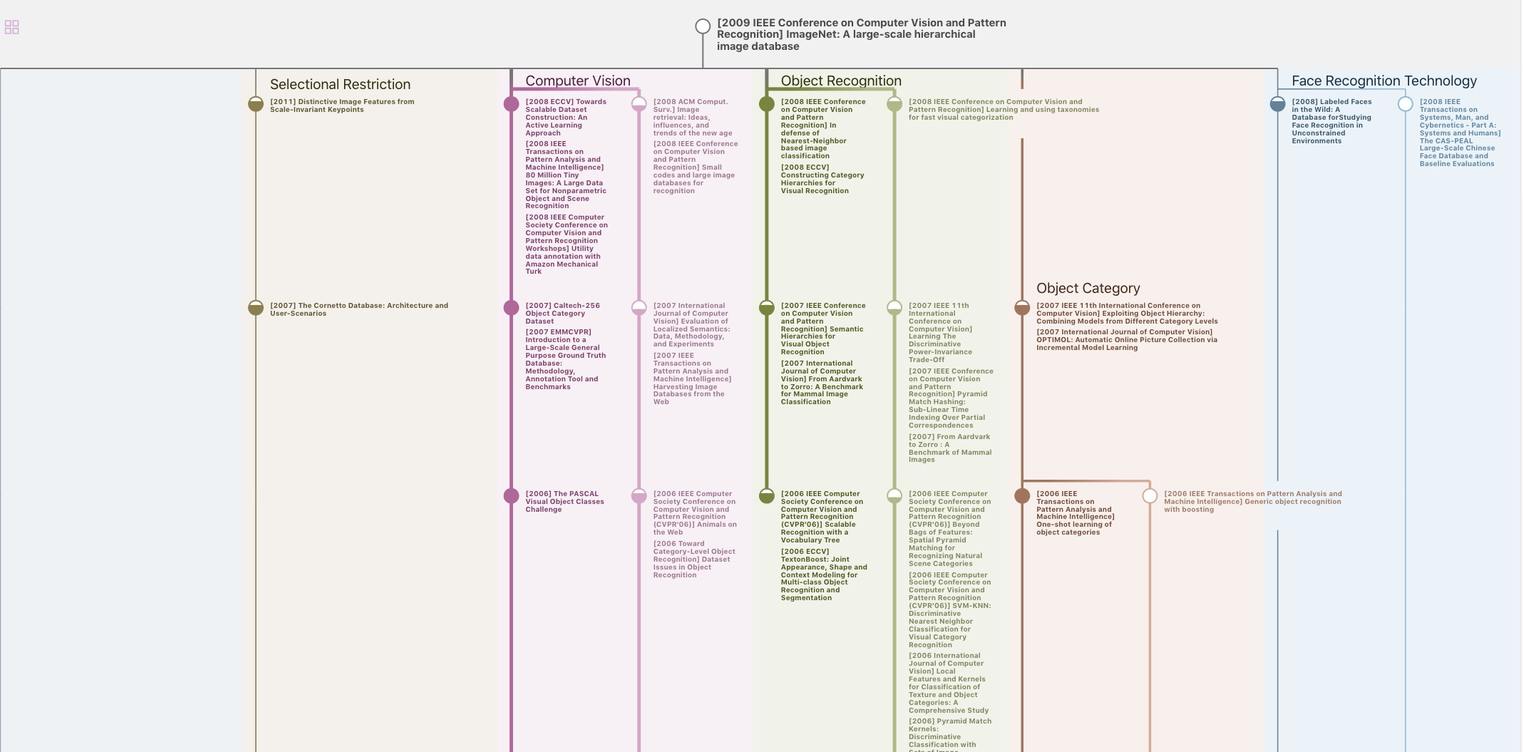
生成溯源树,研究论文发展脉络
Chat Paper
正在生成论文摘要