Research on Suppression Strategy of Plane Distortion in Laser Bending Forming of Specialty-Shaped Corrugated Sheet
Chinese Journal of Lasers(2023)
摘要
Objective The miniaturization and customization of corrugated sheets have become development trends to meet the demand of the high-efficiency heat and mass transfer in methanol reforming microreactors. To avoid problems such as springback, cracking, and wrinkling caused by conventional metal-forming processes, laser-forming technology becomes a potential solution to manufacture such structural components. However, when laser forming is adopted to fabricate specialty-shaped microcorrugated sheets, the sheets are prone to plane distortion defects owing to the uneven distribution of the energy input and free-end constraint in the curved scanning process. The plane distortion may lead to a gap between the corrugated sheets in the microreactor assembly, resulting in fluid leakage and a significant reduction in the heat and mass transfer performance of the microreactor. Because studies focusing on the laser forming of specialty-shaped microcorrugated sheets remain limited, the heat accumulation in laser scanning and the relationship between the temperature field and bending angle with various scanning strategies are analyzed in this study based on numerical simulations and experimental studies. A segmented variable-velocity strategy is explored to suppress the plane distortion. The forming quality of the corrugated sheets is further evaluated. This study provides a reference for the analysis and suppression of the plane distortion in the laser forming of specialty-shaped components. Methods The heat accumulation and temperature field distribution during the laser scanning along a double-arc curve are studied via numerical simulation, and the temperature difference between the top and bottom surface on the scanning path is analyzed using a segmented variable-velocity strategy. An experimental setup for the laser forming of a specialty-shaped corrugated sheet is developed (Fig. 6). The material of the specimen used in the experiments is 304 stainless steel with the size of 65.0 mmx65.0 mmx0.2 mm. A 1.5 kW oscillator continuous fiber laser with a laser power of 250 W and velocity range of 70. 140 mm/s is used. Twelve cycles of scans are performed with the interval time of 10 s. During the experiments, one end of the sheet is fixed with a clamping width of 10 mm and can therefore be turned 180 degrees using a three-jaw chuck. The laser scanning path can be drawn during the experiments and modeling process using the definition of a double-arc specialty-shaped line (Fig. 1). The x-directional and normal-plane bending angles are defined (Fig. 7), and the angles after laser forming are measured using a confocal microscope. Results and Discussions The segmented variable-velocity strategy effectively reduces the heat accumulation in the scanning process along the double-arc curve by discretely controlling the energy distribution along the scanning line. Using the segmented variable-velocity strategy, the heat accumulation at the exit is reduced, and the overall peak temperature decreases (Fig. 3). In addition, the segmented variable-velocity strategy improves the uniformity of the temperature distribution owing to the varying laser irradiation time and heat input (Fig. 5). After the local thermal stress generated during the forming process is balanced by the constraint force of the free end to the laser heating location, a relatively uniform thermal deformation is generated along the scanning line, thereby suppressing the distortion of the forming plane during laser forming. Without considering the heat accumulation, the thermal stress must maintain a downward trend while balancing the binding force at each part of the scanning line (Fig. 4). Combined with the double-layer model, the variation trend of the bending angle of the normal plane depends on the change of the temperature difference ( Fig. 5). The accuracy of the numerical model is verified by comparing the numerical simulation and experiment results of the sheet surface temperature during laser bending forming (Fig. 8). The results demonstrate that a suitable number of velocity-varying segments can balance the energy distribution and reduce the unevenness of the bending angle in the normal plane, whereas the velocity should be set within a reasonable range. The angular difference is reduced to less than 1.0 degrees. The forming efficiency of the corrugated sheet is also improved by using the segmented variable-velocity strategy (Figs. 9 and 10). By using the segmented variable-velocity strategy, the parallelism between the top and bottom surfaces of the corrugated sheet increases by 87.5% and the waviness values of the bottom and wall surfaces decrease by a maximum of 51.2% (Figs. 11 and 12). Conclusions A numerical model for the laser forming of a 304 stainless-steel sheet is developed, and the temperature distribution of the sheet at different numbers of velocity-varying segments is investigated. The results demonstrate that an increase in the segmental velocity can reduce the peak temperature of the top surface and heat accumulation at the exit. Meanwhile, the temperature gradient decreases as the velocity increases. Compared to constant-velocity scanning, the peak temperature at the terminal is significantly reduced by using the segmented variable-velocity strategy. For example, the peak temperature at the exit with eight velocity-varying segments is reduced by 13.4%. The experimental studies based on various scanning strategies and the detection of the normal-plane bending angle demonstrate that the distribution of the normal-plane bending angle is more uniform with an increase in the segmental number and velocity. Owing to the use of the segmented variable-velocity strategy, the forming plane distortion is significantly suppressed and the angle difference is reduced from 5.6 degrees to 1.0 degrees compared to constant-velocity scanning. Furthermore, the parallelism between the top and bottom surfaces of the corrugated sheet increases by 87.5% and the waviness decreases by a maximum of 51.2% by using the suppression strategy. The segmented variable-velocity strategy can be concluded to significantly improve the quality of specialty-shaped corrugated sheet forming.
更多查看译文
关键词
laser technique,laser bending forming,specialty-shaped corrugated sheet,plane distortion,suppression strategy
AI 理解论文
溯源树
样例
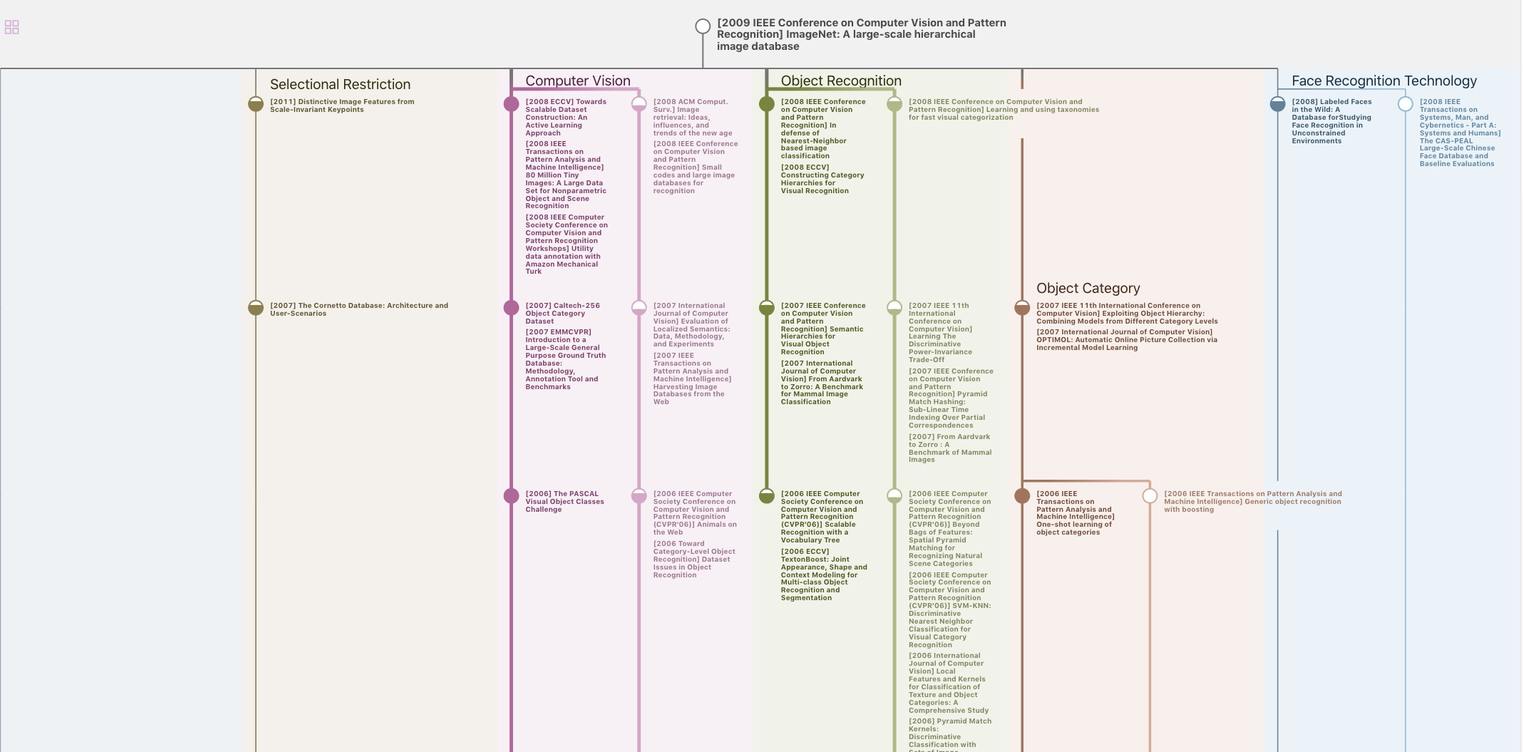
生成溯源树,研究论文发展脉络
Chat Paper
正在生成论文摘要