Analysis of ball milling time to produce self-lubricating copper-tungsten disulfide composite: best trade-off between tribological performance and electrical properties
Next Materials(2024)
摘要
Ball milling is a fundamental step of powder metallurgy widely employed for composite manufacturing. This work focuses on the influence of ball milling time on the morphological, electrical, and tribological properties of self-lubricating copper-tungsten disulfide (Cu-WS2) composites. The study investigates ball milling times between 1 and 24 h to guarantee different degrees of incorporation of WS2 in the copper matrix. Micro-scratch and wear tests are performed to evaluate the tribological behavior. Optical, scanning electron, and confocal laser scanning microscopy analyze the scratch and wear tracks. The results show the reliability of the production process and a general improvement of the composites' mechanical properties compared to pure copper. The addition of WS2 enhances the tribo-mechanical properties, increasing hardness and wear resistance and decreasing the friction coefficient. Shorter ball milling times result in larger WS2 flakes distributed in the copper matrix, while longer ball milling times result in smaller and more dispersed particles. This homogeneous fine dispersion determines a difference in the composites' electrical conductivity and tribological performance, with shorter ball milling times (i.e., between 2 and 4 h) offering the best trade-off between wear behavior and electrical properties.
更多查看译文
关键词
Ball milling,Powder metallurgy,Sintering,Metal matrix composites,Friction,Wear resistance
AI 理解论文
溯源树
样例
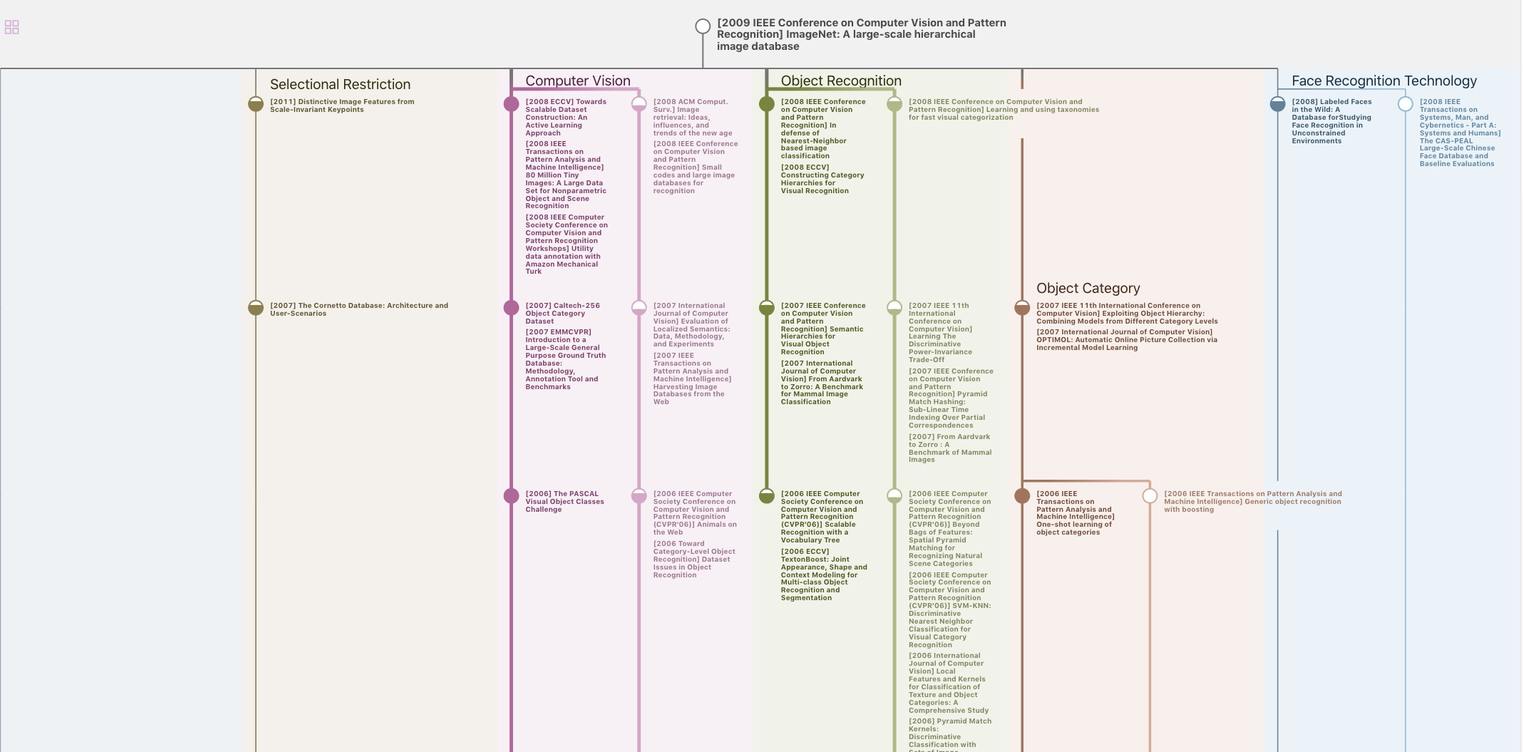
生成溯源树,研究论文发展脉络
Chat Paper
正在生成论文摘要