Fatigue Performance Analysis of Stainless Steel Cruciform Joint with Angular Misalignment
Fatigue & fracture of engineering materials & structures(2024)
Abstract
Welding distortion causes the change of stress distribution of load-carrying cruciform stainless steel welded joints, and the weld with angle less than 90 degrees between steel plates became the fatigue performance control weld because of stress magnification. The effect of angular misalignment on fatigue performance of stainless steel cruciform welded joint was experimentally and numerically studied. The fatigue damage evolution equations, under different stress amplitudes, were derived using relative deformation increment as damage variable based on continuum damage mechanics to explain the process of damage transformation from micro to macro crack and finally rapid fracture. The hot spot stress magnification factor was positively correlated with the welding distortion angle and exhibited two discernible stages of rise and fall with increasing nominal stress taking the proportional limit as boundary. A proposed formula considering both misalignment angle and applied stress aimed to enhance accuracy in fatigue performance evaluation compared to current methods. The fatigue damage evolution process was described by continuum damage mechanics.The Km showed two stages of increase and decrease divided by proportional limit.The calculation formula for the hot spot stress magnification factor was suggested.Suggested method considering angular misalignment was more precise for life prediction.
MoreTranslated text
Key words
continuum damage mechanics,hot spot stress method,stainless steel,welding distortion
AI Read Science
Must-Reading Tree
Example
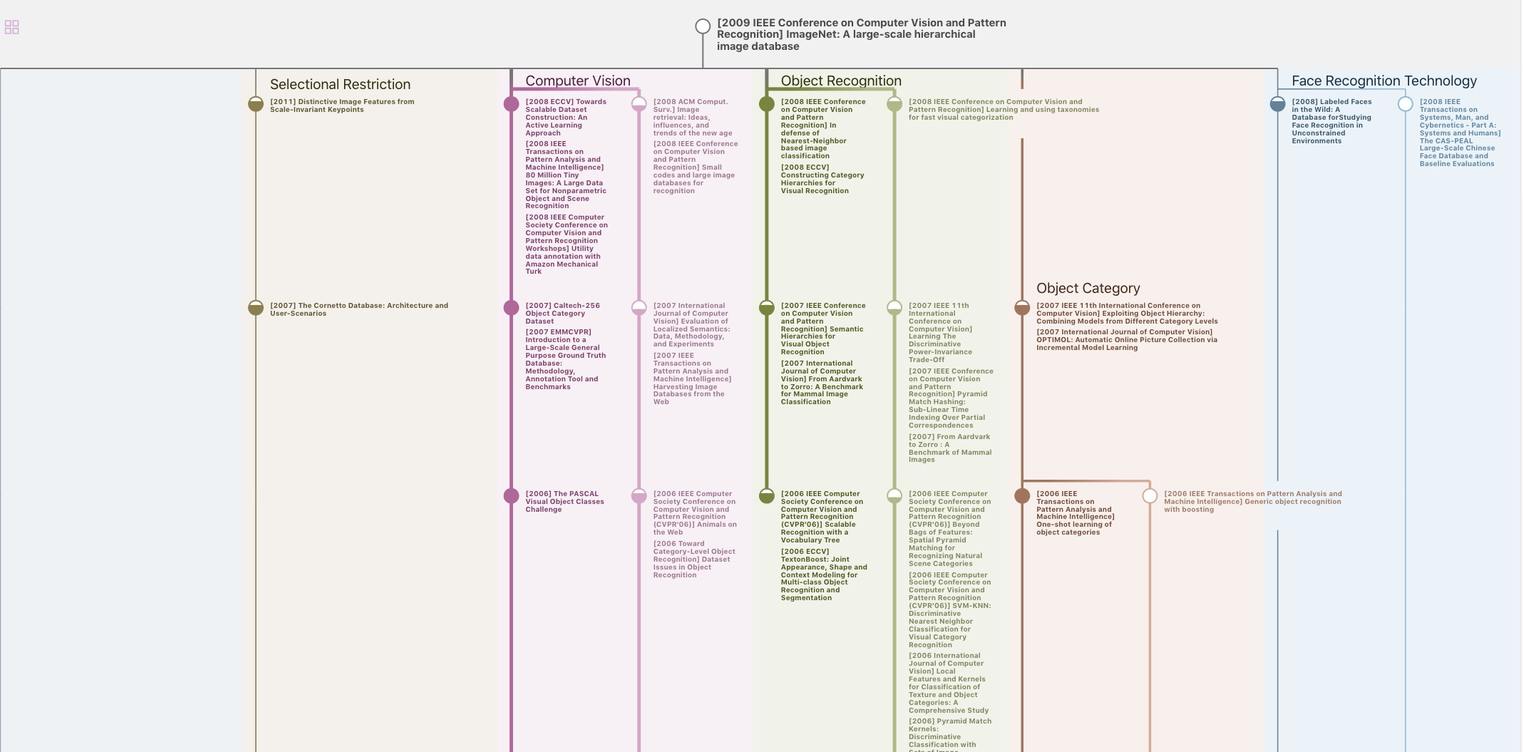
Generate MRT to find the research sequence of this paper
Chat Paper
Summary is being generated by the instructions you defined