Low-Stress Ultrafast Laser Micromachining for High-Frequency PMN–PT/Epoxy Composite Transducers
IEEE Sensors Journal(2024)
摘要
The challenge of achieving micro kerf (<8 μm) for high-frequency (≥30 MHz) composites presents a substantial barrier to the progress of PMN–PT transducers. The ultrafast laser offers a promising avenue for micro- and nano-scale manufacturing, yet the research on the intricate mechanisms underlying their interaction with PMN–PT remains limited. In this study, we proposed and validated a technique involving low-stress ultrafast laser micromachining for the production of high-performance PMN–PT composite array transducers. The optical properties were examined. The interaction mechanisms were explored using a 1.5 ps laser system. The microstructures and elements were comprehensively examined as a function of scanning settings, revealing that less affected regions could be achieved. Furthermore, the mechanical performance, including hardness, elasticity modulus, and stresses, was assessed, demonstrating the potential of achieving low-stress during micromachining. Raman and PFM studies provided evidence that high-performance PMN–PT could be attained post-micromachining. Drawing upon the aforementioned physical models, a prototype 30 MHz PMN–PT composite array transducer was developed to validate the efficacy of low-stress micromachining. The composite showed large electromechanical coupling (>0.72). The transducer exhibited an average center frequency of 29.76 MHz, an average -6 dB bandwidth of 90.5%, and a high peak-to-peak voltage of 746±87 mV at 0 dB gain. We provided valuable insights into the complicated ablation mechanisms generated by ultrafast lasers, which are critical for determining optimal settings, as well as introducing more accessible approaches for producing high-performance PMN–PT composite transducers.
更多查看译文
关键词
low-stress,ultrafast laser,PMN–PT composite transducers,high-frequency
AI 理解论文
溯源树
样例
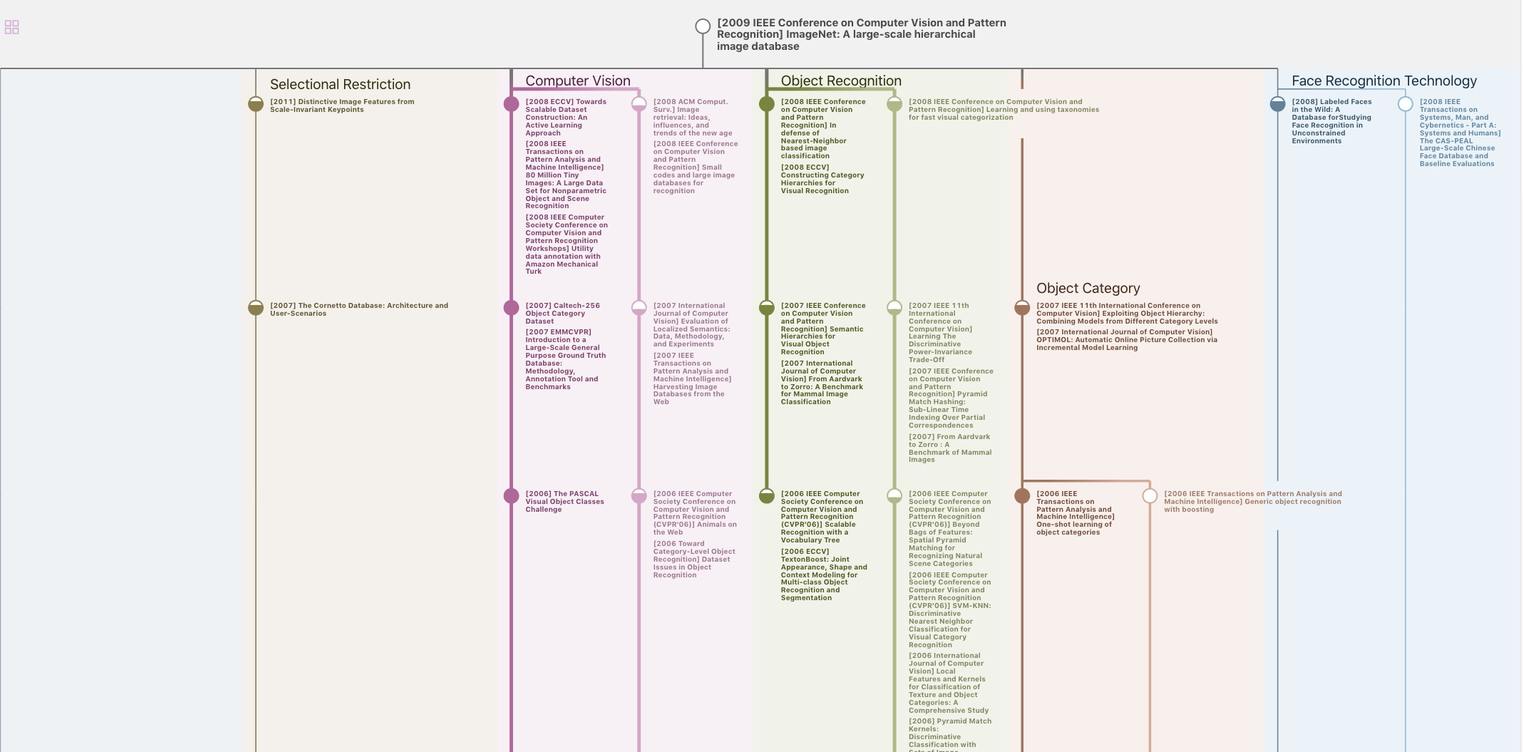
生成溯源树,研究论文发展脉络
Chat Paper
正在生成论文摘要