Evolutions of Multidimensional Wear Features in Ball-End Milling of Ni-based Superalloy GH4169
The international journal of advanced manufacturing technology/International journal, advanced manufacturing technology(2024)
Abstract
Tool wear is one of the factors restraining the improvement of product efficiency and machining quality, especially for the aerospace industries with high-added-value parts and hard-to-cut material. During the finish milling of the free-form surface, tool orientations and engagement regions constantly change, which renders the traditional average flank wear hard to describe the tool wear condition accurately. In the present work, tool wear in multiple dimensions is studied comprehensively by using solid carbide ball-end mills with different lend angles, and it is designed by a fixed GH4169 workpiece in various angles. The results show that flank wear, wear depth, wear area, and wear volume increase with the cutting length. The relationship between cutting parameters and those wear features was analyzed with the variance and cluster analysis. The rates of wear area and wear volume were more sensitive to cutting parameters compared to flank wear. What’s more, wear volume was affected significantly by all the main effects and some intersections of those factors, that is, spindle speeds, feeds, lead angles, and initial flank wear, which gave the maximum information in distinguishing the effects of cutting parameters. From the perspective of statistics, 36.1% of cases owned higher wear rates in cluster analysis for the stochastic wear process.
MoreTranslated text
Key words
Tool wear,Superalloy,Milling,Ball end mill,Sculptured surface
AI Read Science
Must-Reading Tree
Example
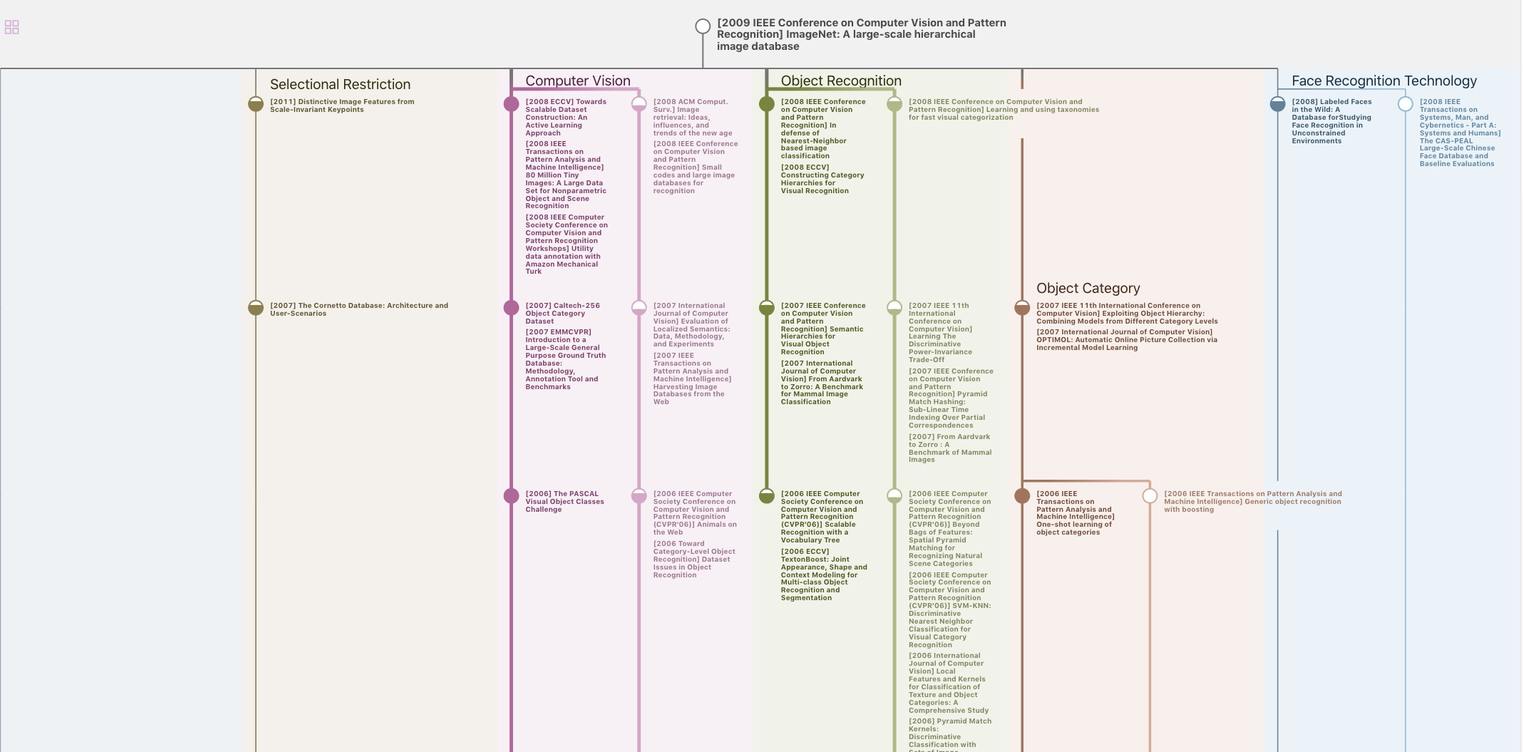
Generate MRT to find the research sequence of this paper
Chat Paper
Summary is being generated by the instructions you defined