A calibration and compensation method for an industrial robot with high accuracy harmonic reducers
Science China Technological Sciences(2024)
摘要
Industrial serial robots need high stiffness to keep absolute pose accuracy and meet the requirements in practical applications. However, the weak stiffness feature of robot joints and the payloads affected on robot end-effector, which will also increase the pose error of robot. Especially, the existing calibration methods often consider under no-payload condition without discussing the payload state. In this paper, we report a new industrial serial robot composed by a new harmonic reducer: Model-Y, based on high accuracy and high stiffness, and a kinematic parameter calibration algorithm which is based on a harmonic reducer force-deformation model. To decrease the accuracy effects of payload, an iterative calibration method for kinematic parameters with payload situation was proposed. Simulation and experiments are conducted to verify the effectiveness of the proposed calibration method using the self-developed industrial serial robot. The results show a remarkably improved accuracy in absolute position and orientation with the robot’s payload range. The position mean error has 70% decreased to 0.1 mm and the orientation mean error diminished to less than 0.01° after calibration with compensation. Additionally, online linear and circular tests are carried out to evaluate the position error of the robot during large-scale spatial and low-speed continuous movement. The accuracy is consistent with the previous calibration results, indicating the effectiveness and advantages of the proposed strategy in this article.
更多查看译文
关键词
industrial serial robot,Model-Y harmonic,calibration,stiffness model,online compensation
AI 理解论文
溯源树
样例
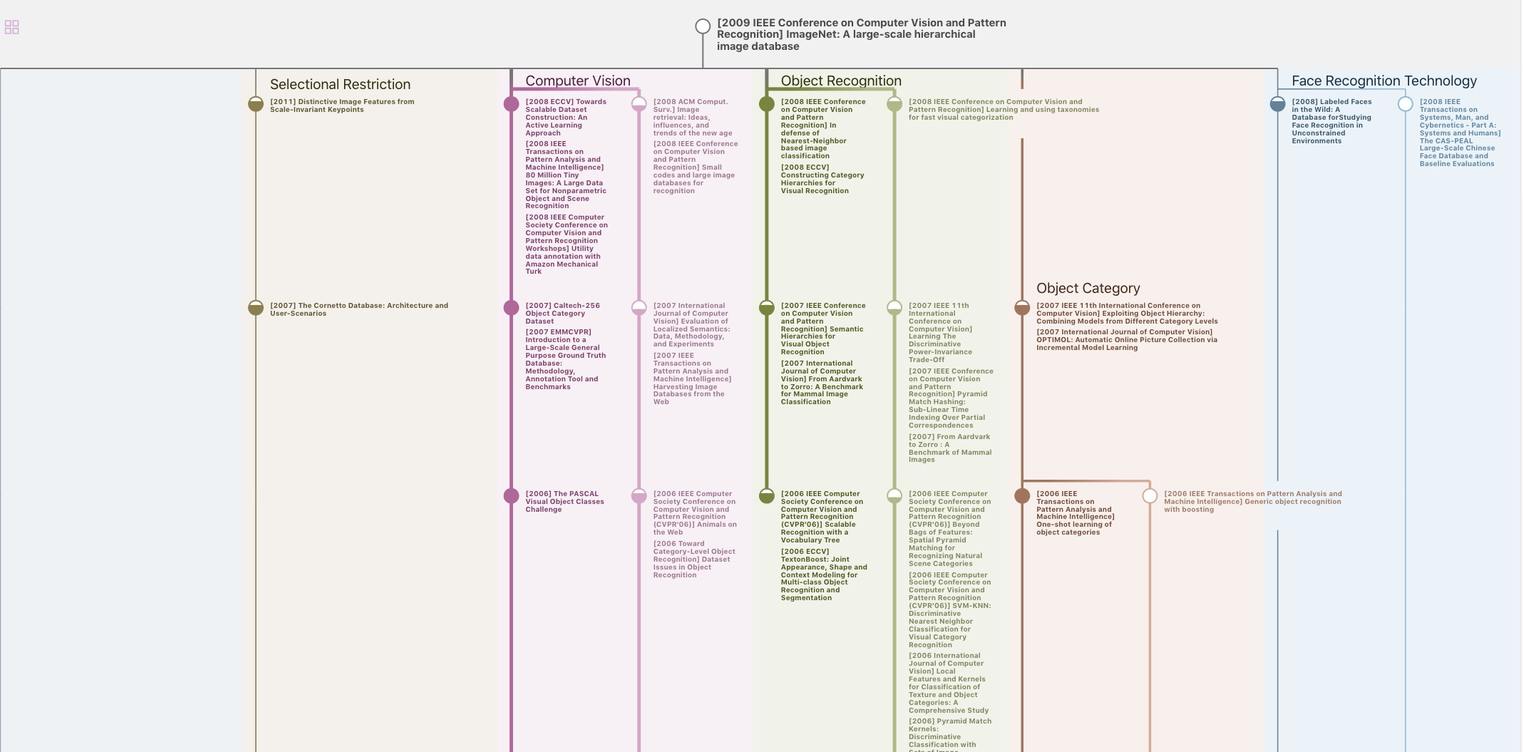
生成溯源树,研究论文发展脉络
Chat Paper
正在生成论文摘要