Surface Residual Stress and Roughness Mapping for Different Build Locations in Laser Powder Bed Fusion of Maraging Steel
Journal of Materials Engineering and Performance(2024)
摘要
Metal laser powder bed fusion (L-PBF) technologies are being massively studied to achieve a broader implementation of their advantages over subtractive techniques. L-PBF benefits the development of components with high-performance and lightweight structures because of the layerwise approach, providing disruptive manufacturing. One main challenge in L-PBF is producing parts with controllable residual stresses naturally generated during materials processing. The complex thermal cycle experienced by the material during L-PBF manufacturing makes managing and controlling this feature even more challenging. This study investigated the effect of different build locations on the surface residual stress and roughness of maraging steel samples manufactured by L-PBF. X-ray diffraction (XRD) for residual stress assessment and area roughness ( S a ) measurements using a confocal laser scanning microscopy (CLSM) allowed the mapping of these critical properties. Average surface residual stress varied up to 55% on the upward surface. Also, the residual stress profile on the side of the samples highlighted dependence on the measurement height along the build direction and the build platform location. The latter influence was also identified for S a results. Therefore, the results bring insights into the process planning relevance for the final residual stress in L-PBF manufactured components.
更多查看译文
关键词
additive manufacturing,build platform location,laser powder bed fusion,nondestructive testing,residual stress,roughness
AI 理解论文
溯源树
样例
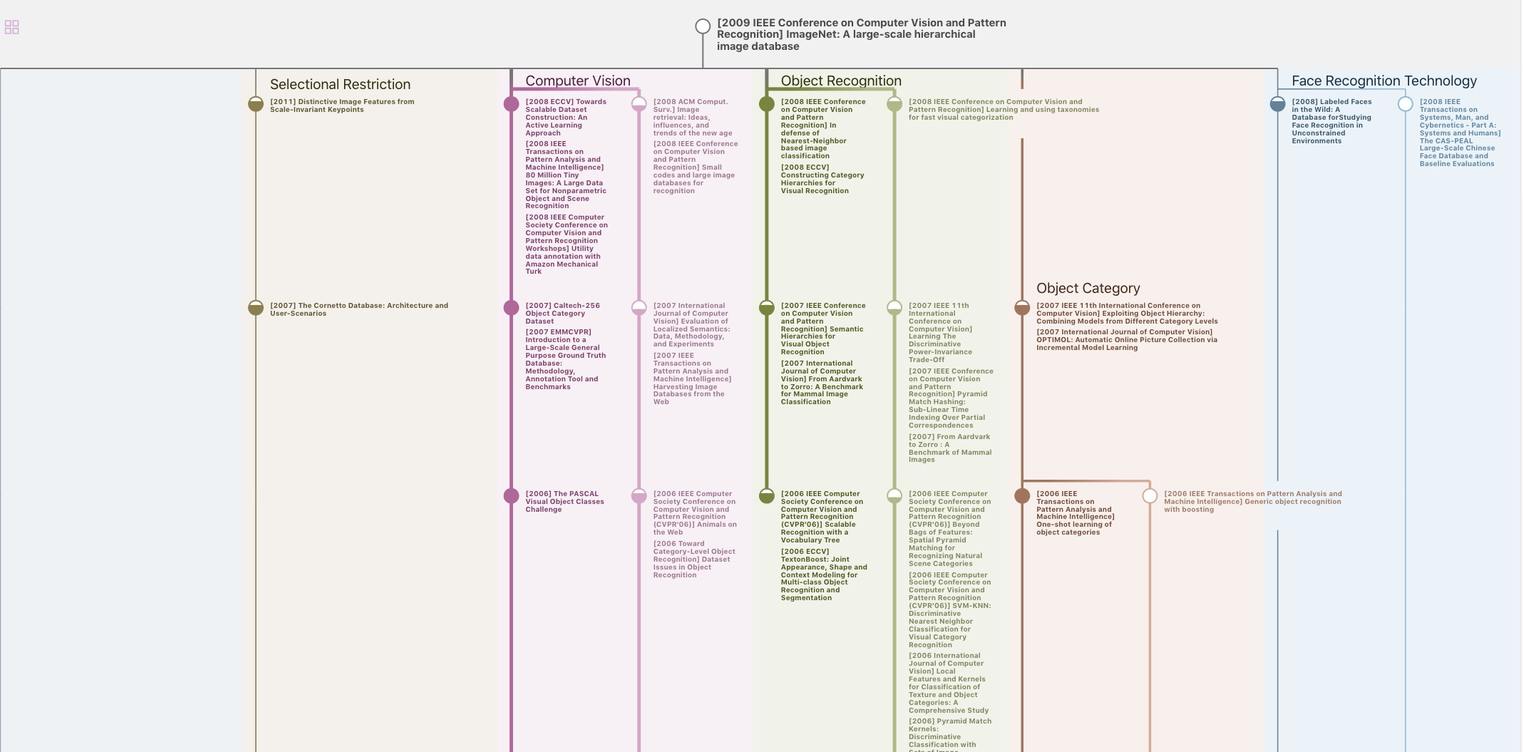
生成溯源树,研究论文发展脉络
Chat Paper
正在生成论文摘要