Enhancing mechanical and damping performance of 3D-printed aluminium-7075 with shape memory high-entropy alloy (SMHEA): parametric optimization and mathematical modeling
INTERNATIONAL JOURNAL OF ADVANCED MANUFACTURING TECHNOLOGY(2024)
摘要
In this study, we examined the applicability of a response surface approach in the experimental design, parametric optimization, and formulation of predictive models in the 3D printing of aluminium-7075/Ti48Zr20Hf15Al10Nb7 shape memory high-entropy alloy (SMHEA) composite. The input variables consist of the SMHEA dosage (A), laser power (B), and powder flow rate (C), which vary from 2 to 8 wt%, 400 to 800 W, and 1.44 to 7.2 g/min, respectively. In the meantime, the yield strength, tensile ductility and modulus, hardness, damping capacity, and loss modulus were examined. The ANOVA results indicated that the input variables A, B, and C had significant effects on the responses, resulting in mathematical models with a high degree of fitness that adequately represented the experimental outcomes. Optimal parametric optimization was achieved at 6.4 wt%, 388 watts, and 3.6 g/min with a desirability of 0.916%. Comparing the predicted responses to the validation results under optimal conditions revealed a deviation < +/- 5%, validating the models' potency to predict the responses. Thus, optimal parametric conditions for the development of a 3D-printed aluminum-7075/Ti48Zr20Hf15Al10Nb7 composite were confirmed to be adequate.
更多查看译文
关键词
3D printing,Additive manufacturing,Damping performance,Metal composite,Powder flow rate, Shape memory high-entropy alloy
AI 理解论文
溯源树
样例
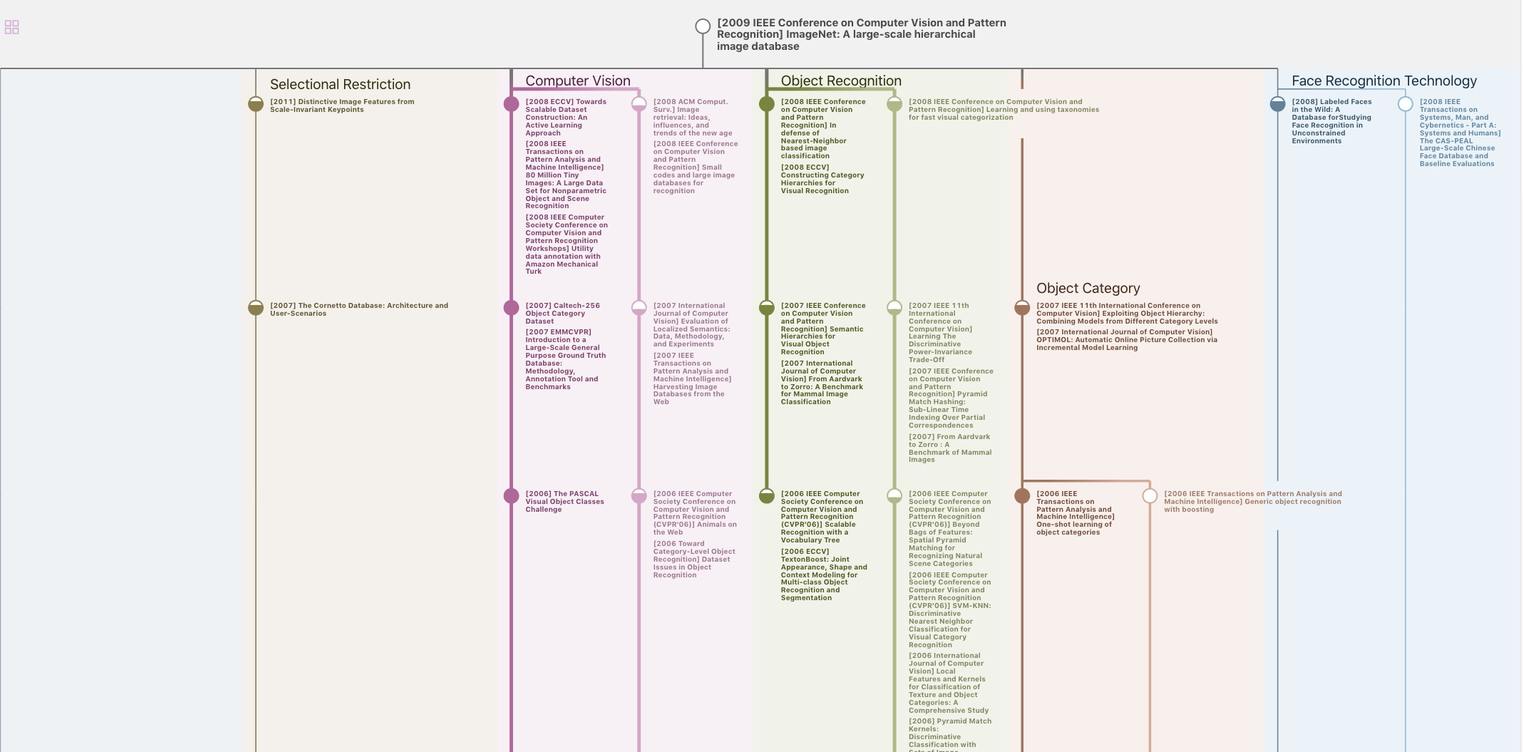
生成溯源树,研究论文发展脉络
Chat Paper
正在生成论文摘要