Comparative investigation and optimization of cutting tools performance during milling machining of titanium alloy (Ti6Al4V) using response surface methodology
The International Journal of Advanced Manufacturing Technology(2024)
摘要
The purpose of this paper is to study the optimization of the cutting performance of three different cutting inserts, during the machining operation of titanium alloy (Ti6Al4V) by making use of the response surface methodology (RSM) on a computer numerical control (CNC) milling. The cutting tools employed for the optimisation of the cutting performance during machining operation are silicon, aluminium, oxygen, nitrogen (SiAlON), cubic-boron nitride and carbide cutting inserts. Scanning electron microscope (SEM) was used for the determination of the tool wear for the cutting inserts being compared during machining of Ti6Al4V, and the cutting parameters, which are cutting speed ( V c ), feed per tooth ( f z ) and depth-of-cut that were evaluated from the cutting tools as per the manufacturer’s design specifications. The determination of the tool wear on the cutting inserts was achieved by using the SEM, while the machining operation for the experimental trails was performed from the CNC milling machine, where face milling operation was executed. The optimization process showed that carbide cutting inserts yielded the best performing results and were considered the most significant choice of cutting insert in machining Ti6Al4V when compared to SiAlON and CBN cutting inserts. This choice was from the cutting tool life obtained where a cutting tool life of 29 min was obtained from a use of carbide cutting inserts; 28 min resulted from a use SiAlON cutting inserts and 26 min from a use of CBN cutting inserts. This work finds appropriate value in assisting the machinists in the selection of the best most performing and cost-effective cutting tool.
更多查看译文
关键词
Cutting speed,CNC milling machine,Cutting inserts,Face milling,Tool wear and titanium alloy
AI 理解论文
溯源树
样例
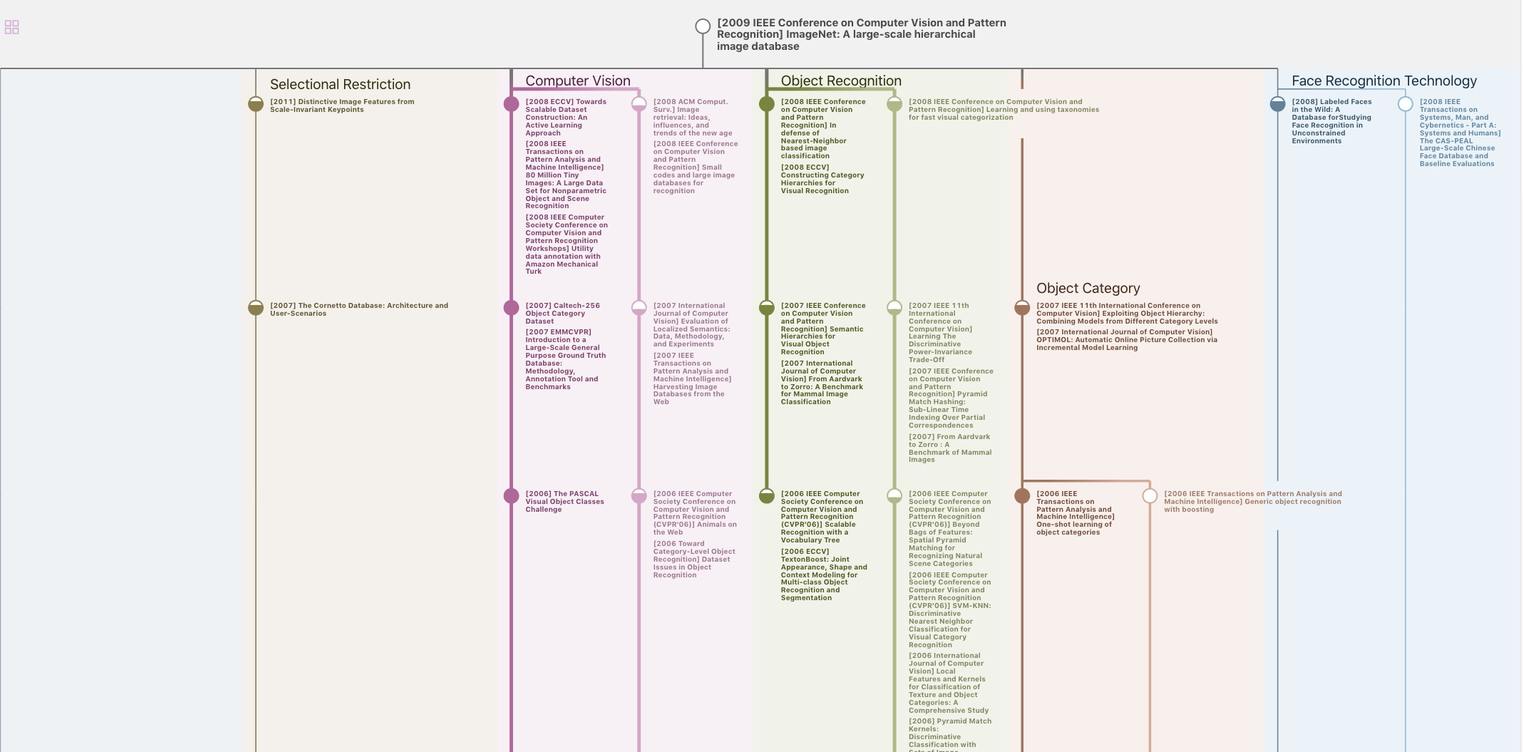
生成溯源树,研究论文发展脉络
Chat Paper
正在生成论文摘要