Integrated Planning of Multiple Spare Parts Inventory, Warranty, and Service Engineers for a Service-Oriented Manufacturer
IEEE TRANSACTIONS ON AUTOMATION SCIENCE AND ENGINEERING(2024)
摘要
This paper considers a service-oriented manufacturer providing products and associated after-sales maintenance service with a warranty period to customers. The manufacturer gains revenue from both product sales and after-sales maintenance service which are affected by the warranty period length. The arrival tendency of customers for after-sales maintenance service is higher during the warranty period than that after the warranty expires. The manufacturer repairs stochastic failures of products with both spare parts of the right kind and employed service engineers. If the spare part is not available upon repair demand, the manufacturer can resort to the emergency suppliers (e.g., OEMs). We establish an original decision model for the service-oriented manufacturer and analytically derive the arrival rates of service demand under and out of warranty, and the repair call rates for requiring regular and emergency replenishment based on queuing theory. Then, a computationally efficient algorithm is designed to obtain the joint multiple spare parts inventory, service engineer employment and warranty period decisions. Numerical studies show that both the manufacturer and customers can benefit from the longer warranty period when customers are more inclined to require maintenance service out of warranty from the manufacturer. A higher service level target or quality levels of spare parts reduce the after-sales service dependence on emergency suppliers. Note to Practitioners-After-sales maintenance services often generate significant profit for many service-oriented manufacturers that sell products bundled with after-sales services. To offer efficient after-sales maintenance services, efficient joint management of spare part inventory, service engineers and warranty periods, which often interact with each other, is crucial for service-oriented manufacturers. However, in practice, facing the stochastic arrival of repair calls, it is challenging for manufacturers to jointly optimize the decisions of spare parts inventory, service engineers and warranty periods. Most existing studies optimized them separately. This research investigates the joint decision problem considering the three aspects based on queuing model. Based on the model analysis, an efficient and easy-to-implement heuristic algorithm is proposed to obtain reasonable joint decisions. Practitioners can implement the proposed approach to improve the integrated planning of spare parts inventory, warranty and service engineers and enhance profitability. Besides, sensitivity analysis is conducted to show how the changes of parameters such as payment to the supplier per emergency shipment and rate of the component lifespan will affect the joint decisions. Some managerial insights obtained can be useful to practitioners. First, if customers become more willing to require maintenance service from the manufacturer out of warranty, the manufacturer can benefit more from extending the warranty period length which is also beneficial to customers, leading to a win-win situation. Second, if the emergency replenishment cost becomes higher, the manufacturer should extend the warranty period length. Third, a higher service level target or quality levels of spare parts decline the dependence of the after-sales service on emergency suppliers.
更多查看译文
关键词
Warranties,Maintenance engineering,Costs,Planning,Inventory management,Employment,Stochastic processes,After-sales maintenance,spare parts management,service engineers,warranty
AI 理解论文
溯源树
样例
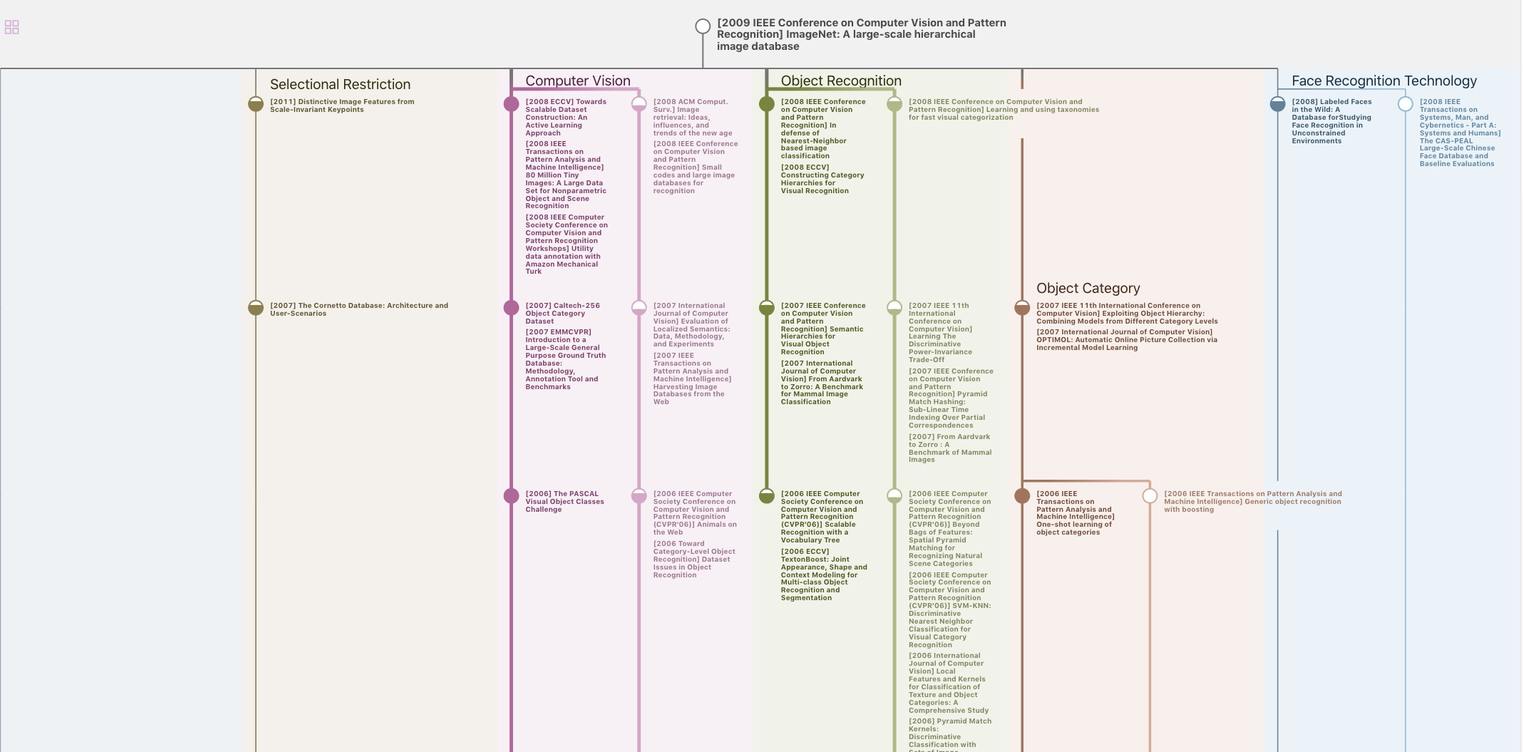
生成溯源树,研究论文发展脉络
Chat Paper
正在生成论文摘要