Crack propagation in adhesive bonded 3D printed polyamide: Surface versus bulk patterning of the adherends
INTERNATIONAL JOURNAL OF ADHESION AND ADHESIVES(2024)
摘要
The confined build space of 3D printers often necessitates breaking down larger objects into sub-components for efficient printing. Addressing this challenge, related existing research emphasizes the growing adoption of structural adhesives as a key method for joining 3D printed components. In this context, the present study combines finite element modeling, design exploration, and additive manufacturing, to ascertain the role of the adherends' architecture on the mechanics of crack growth in adhesive bonded 3D printed materials. Finite element simulations and experiments are carried out using Double Cantilever Beam (DCB) specimens comprising epoxy-bonded selective laser sintered polyamide (PA). In particular, the study includes adherends that feature either sub-surface hollow channels of various shapes (bulk patterns) or sinusoidal interfaces with different aspect ratios (surface patterns). The objective is to demonstrate how the proposed patterning strategies not only promote crack shielding and delayed growth but also unlock energy-absorbing processes, such as interfacial void growth and buckling, that are absent in the control joint (i.e., no patterns). Therefore, customizing the architecture of the adjoined layers ultimately results in toughening and enhanced damage tolerance in adhesive joints that comprise 3D printed materials.
更多查看译文
关键词
3D printing,Adhesive bonding,Double cantilever beam,Cohesive model,Crack trapping
AI 理解论文
溯源树
样例
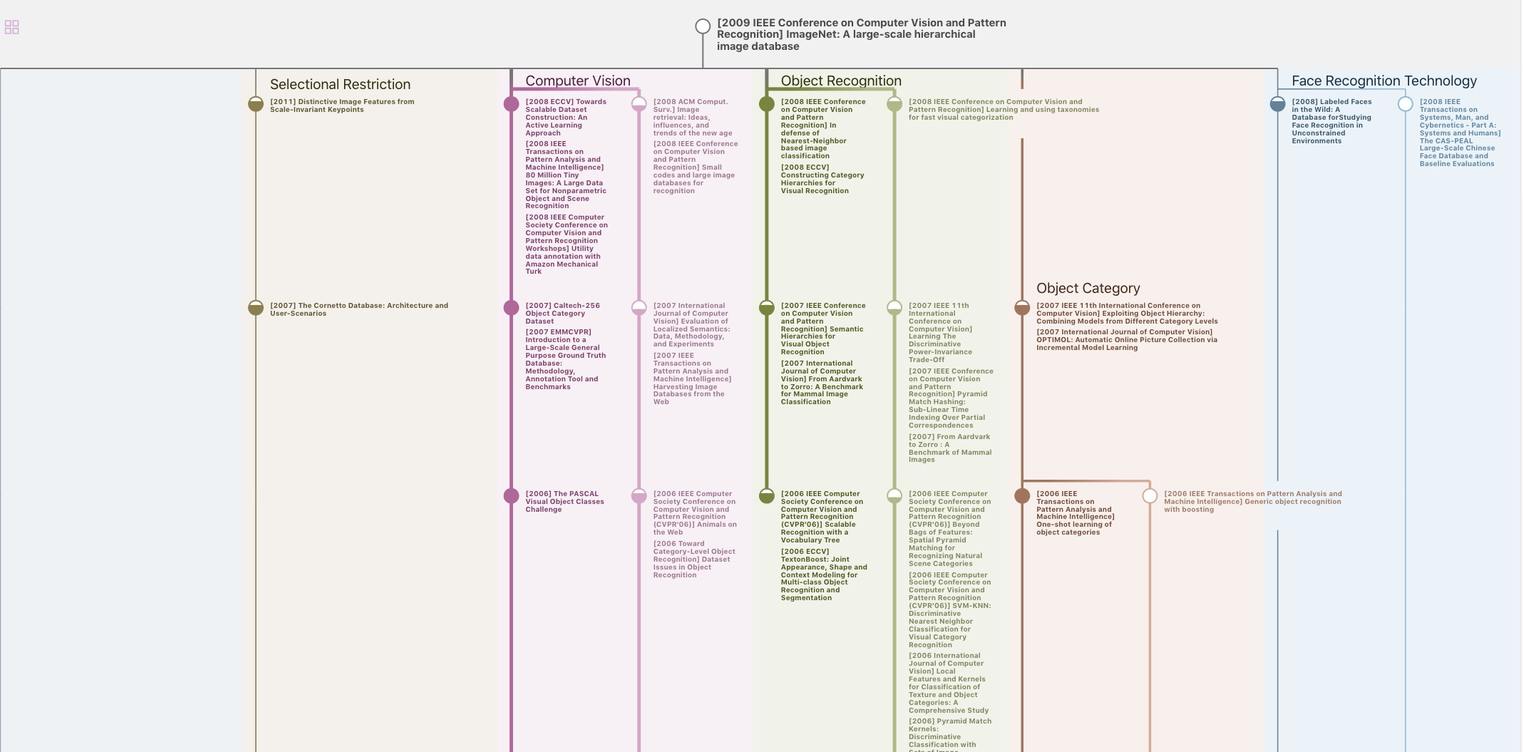
生成溯源树,研究论文发展脉络
Chat Paper
正在生成论文摘要