Comparison of drilling of Inconel 625 by AWJM and WEDM
AIRCRAFT ENGINEERING AND AEROSPACE TECHNOLOGY(2024)
摘要
PurposeThis study aims to comparatively analyze the cut parts obtained as a result of cutting the Ni-based Inconel 625 alloy, which is widely used in the aerospace industry, with the wire electro-discharge machining (WEDM) and abrasive water jet machining (AWJM) methods in terms of macro- and microanalyses.Design/methodology/approachIn this study, calipers, Mitutoyo SJ-210, Nikon SMZ 745 T, scanning electron microscope and energy dispersive X-ray were used to determine kerf, surface roughness and macro- and microanalyses.FindingsConsidering the applications in the turbine industry, it has been determined that the WEDM method is suitable to meet the standards for the machinability of Inconel 625 alloy. In contrast, the AWJM method does not meet the standards. Namely, while the kerf angle was formed because the hole entrance diameters of the holes obtained with AWJM were larger than the hole exit diameters, the equalization of the hole entry and exit dimensions, thanks to the perpendicularity and tension sensitivity of the wire electrode used in the holes drilled with WEDM ensured that the kerf angle was not formed.Originality/valueIt is known that the surface roughness of the parts used in the turbine industry is accepted at Ra = 0.8 mu m. In this study, the average roughness value obtained from the successful drilling of Inconel 625 alloy with the WEDM method was 0.799 mu m, and the kerf angle was obtained as zero. In the cuts made with the AWJM method, thermal effects such as debris, microcracks and melted materials were not observed; an average surface roughness of 2.293 mu m and a kerf of 0.976 degrees were obtained.
更多查看译文
关键词
Ni-based superalloy,Machinability,AWJM,WEDM,Surface integrity
AI 理解论文
溯源树
样例
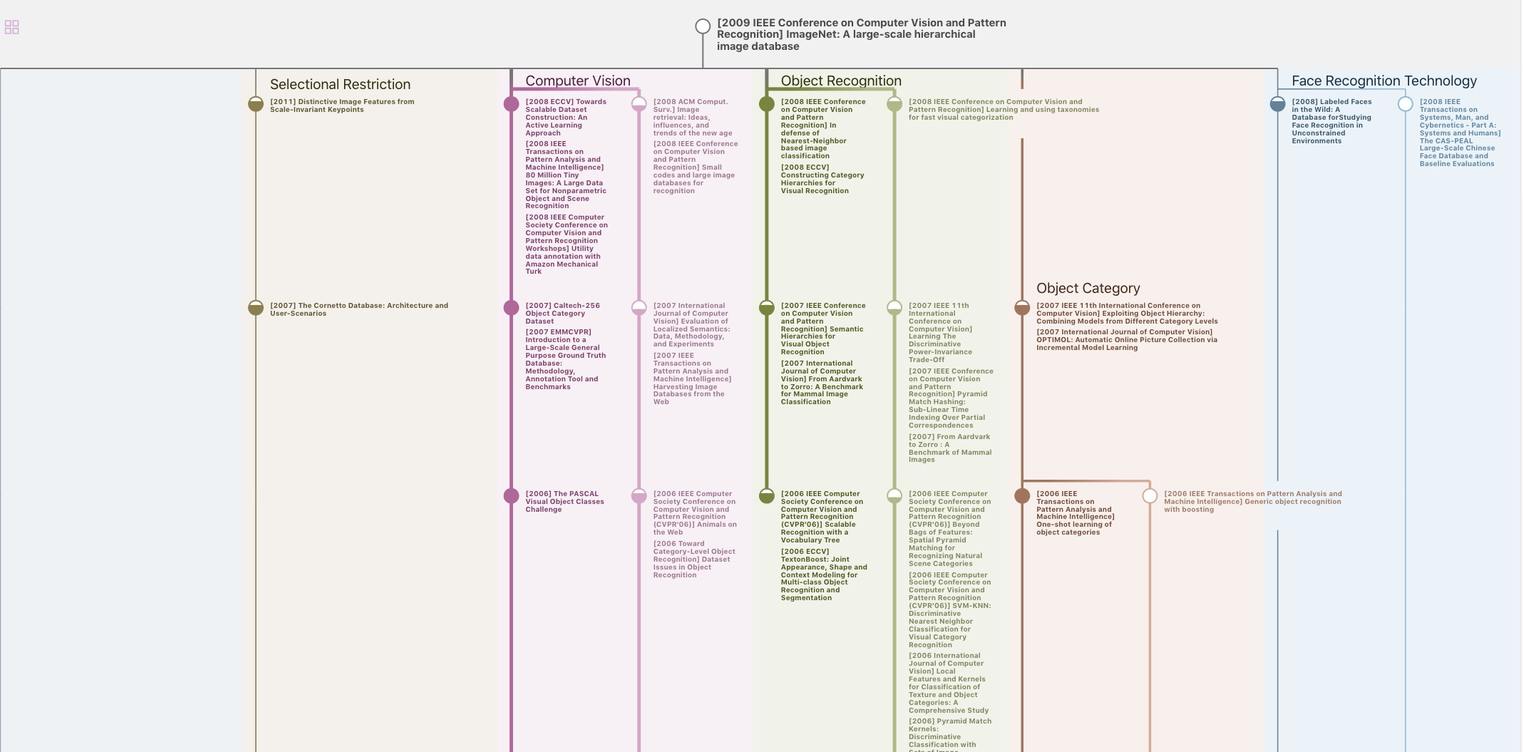
生成溯源树,研究论文发展脉络
Chat Paper
正在生成论文摘要