Optimization of natural rubber foams: Effect of foaming agent content and processing conditions on the cellular structure and mechanical properties
Cellular Polymers(2024)
摘要
In the past decades, natural rubber (NR) foams became popular in the automotive, construction and aerospace industries because of their lightweight, flexibility and shock-absorbing properties. The selection of optimal formulation and processing parameters is critical to produce foam with specific properties depending on the application. In this study, the effect of foaming agent concentration, foaming temperature and time on the morphological and mechanical properties of NR foams was investigated. First, increasing the foaming agent content from 5 to 9 phr (parts per hundred rubber) increased the cell size (16%), while decreasing the compression modulus (28%). In the second part, increasing the foaming temperature (145 to 155°C) resulted in larger cell size (163%); while decreasing the cell density (28%), compression modulus (2%), and hardness (1%). In the third part, increasing the foaming time (25 to 45 min) led to smaller cell size (63%) combined with higher cell density (100%), compression modulus (16%), and hardness (3%). Based on all the results obtained, the best NR foam was obtained with 7 phr of foaming agent and produced at 150°C for 35 min leading to superior morphological and mechanical performance: the smallest cell size (25 µm) and the most uniform cell size distribution ( Đ = 1.03) generating the highest compression modulus (3.36 MPa). Finally, the experimental compression results were combined to build a nonlinear regression model to optimize the formulation and processing conditions leading to 6.5 phr of OBSH molded at 150°C for 36 min. The model showed good agreement with a validation test with less than 2% deviation observed for both compression modulus and strength.
更多查看译文
AI 理解论文
溯源树
样例
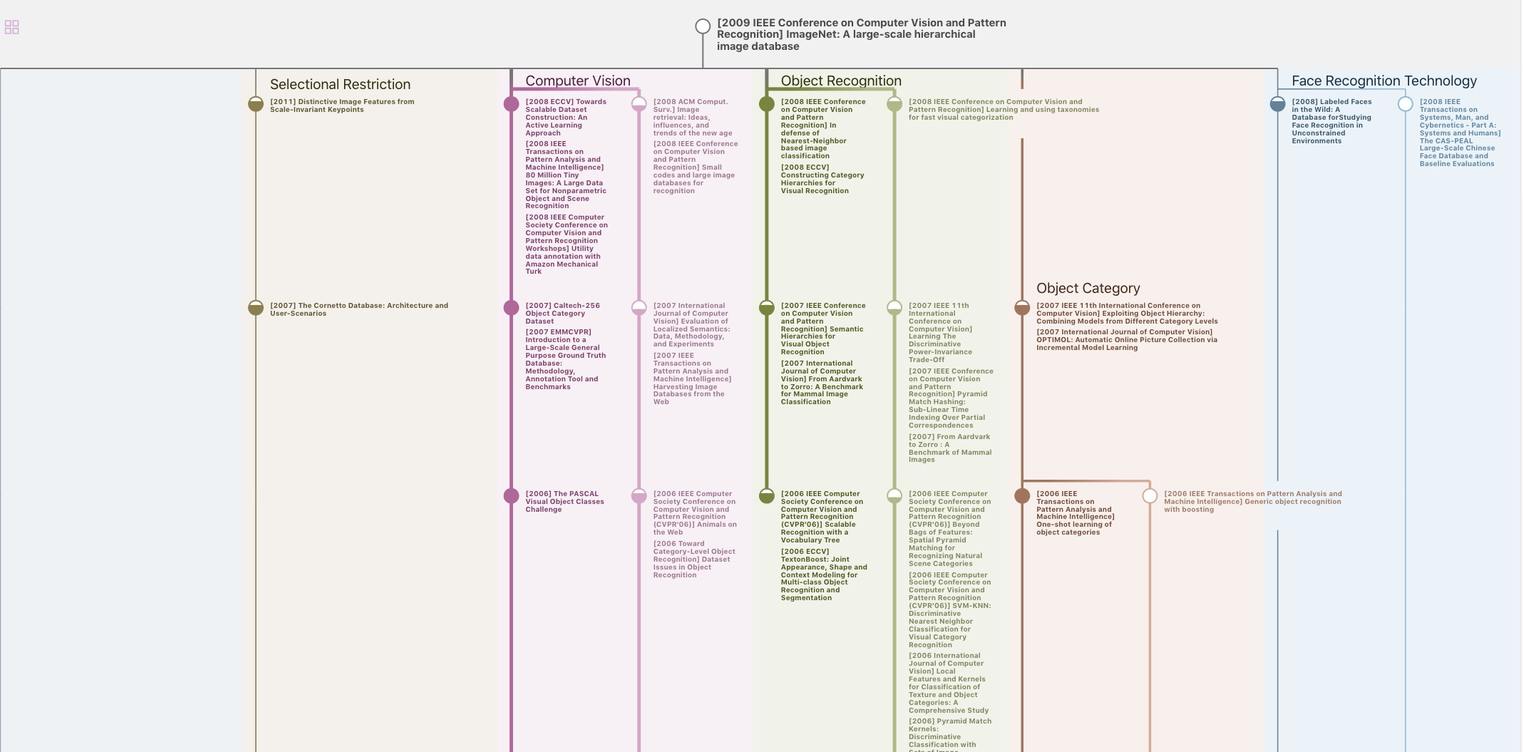
生成溯源树,研究论文发展脉络
Chat Paper
正在生成论文摘要