Impact of catalyst carrier with TPMS structures on hydrogen production by methanol reforming
INTERNATIONAL JOURNAL OF HYDROGEN ENERGY(2024)
摘要
As the core part of a microreactor, the reaction carrier provides reaction site and energy supply for hydrogen production. Among various types of reaction carriers, porous reaction carriers with complex flow path structures can effectively improve hydrogen production performance, and thus are widely applied in fuel cells. To optimize the structure of catalyst carriers and improve the efficiency of hydrogen production of methanol reforming, we designed four TPMS porous carrier structures, namely structures D, G, P and IWP, and analyzed the effect of carrier structure and parameters on hydrogen production reaction in theory. After that, we manufactured TPMS carriers with varied structures and parameters using 3D printing, and designed and carried out loading tests, flow velocity simulation experiments and pressure drop calculation to study the influence of the structure morphology on load intensity, heat and mass transfer and other performance indexes with catalyst load. Finally, we carried out hydrogen production experiments in microreactors with different TPMS structures, from which we obtained an pattern influence of hydrogen production conversion rate and hydrogen velocity etc. At different velocities and temperatures. The experimental results indicate that structure type and parameters of TPMS node and porosity have a great effect on the performance of hydrogen production. Specifically, structure D performs the best and structure P performs the worst in hydrogen production. When the velocity is 1.7 ml/h and the temperature is 250 degrees C, the maximum difference of the hydrogen conversion rate between D and P structure can reach to 22 %, and that of the hydrogen velocity can reach to 0.02 mol/h.
更多查看译文
关键词
3D printing,TPMS structures,Loading of catalyst,Heat and mass transfer,Hydrogen production
AI 理解论文
溯源树
样例
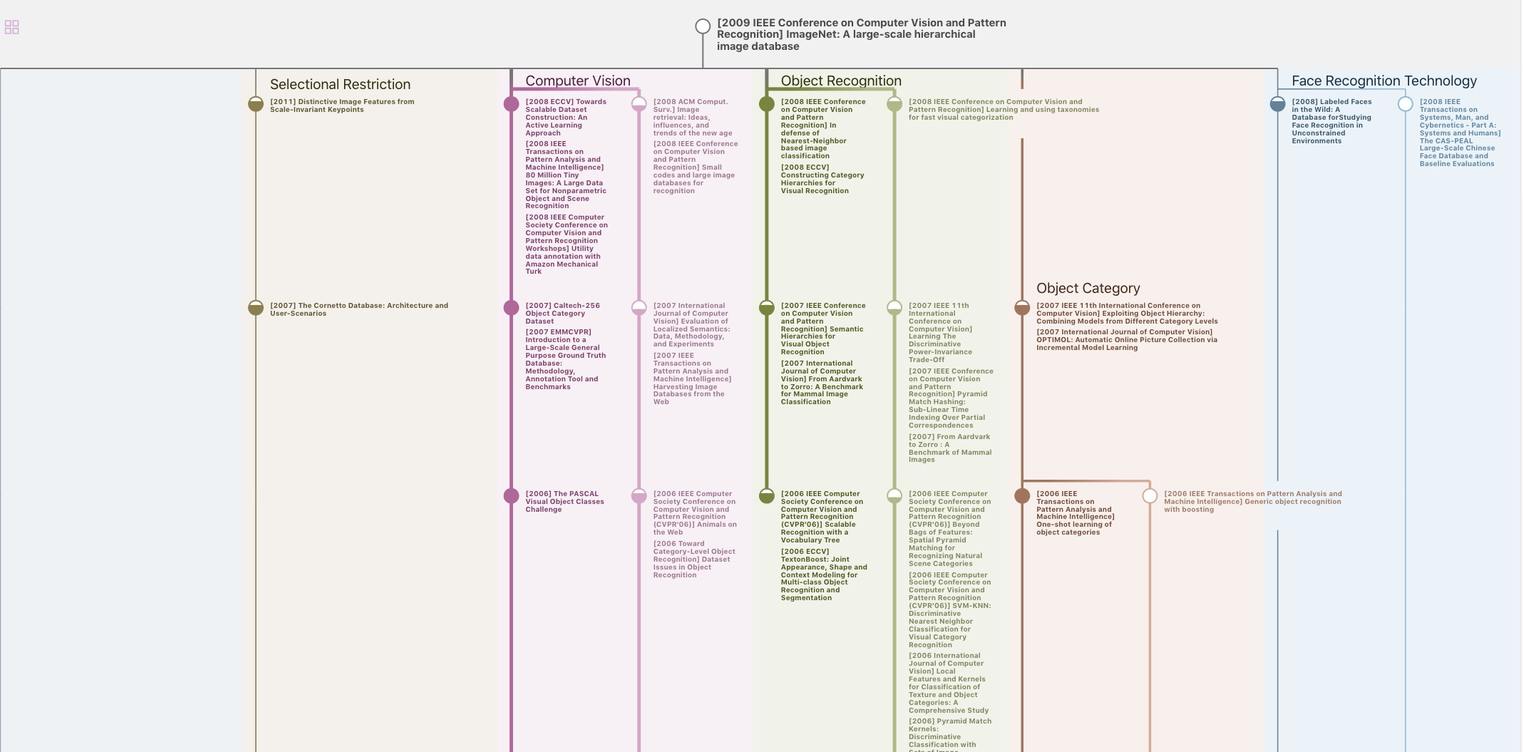
生成溯源树,研究论文发展脉络
Chat Paper
正在生成论文摘要