An investigation into the relationship between hemisphere tooling parameters and thickness changes during the thermoforming of a thermoplastic composite
Materials Research Proceedings Material Forming: ESAFORM 2024(2024)
摘要
Abstract. Thermoforming is an economical and fast means of transforming a flat sheet of thermoplastic composite material into a complex shape. The two-step process consists of a preform phase that transforms the laminates to near net shape ply stacks and of a subsequent consolidation step that employs pressure and heat to join the preforms into a final part. During the preform step, many aspects of the process must be regulated to minimize undesirable affects. A binder ring applies pressure to the material to induce in-plane tension, aiding in the initiation of shear deformation in the laminate. The material increases in thickness as it undergoes in-plane shear to conform to the preform shape. The degree of shear varies over the part, creating variations in thickness and subsequent challenges with uniform consolidation. While material attributes and processing parameters are critical in successful preforming, refining the tool geometry can also lead to significant changes in the preform outcome. Although many of these challenges have been addressed in a design-build-test approach, the goal of this research is to develop a virtual process that can guide design changes in the tooling to achieve a well consolidated part. A discrete mesoscopic modeling approach was implemented in LS-DYNA using thickness-change shell elements (ELFORM25) that can incorporate 3D material properties, including through-plane thickness changes. The current state of the simulation effectively incorporates material behavior, tool/ply friction and thickness changes that reflect variations in pressure. The simulation is used to investigate the significance of the punch/die gap size and the die fillet radius on the tooling geometry. The modeling approach was verified through comparison to experimental results with two types of tooling geometry. A parametric study was then performed to investigate tooling changes in relation to the number of layers, or thickness, of a unidirectional ultra-high molecular weight polyethylene (UHMWPE) material, DSM Dyneema® HB210. The outcomes of the result were evaluated by comparing wrinkle formation, shear deformation and thickness variations. The research shows that the radius of the die fillet has a significant impact on the uniformity of thickness in the preform. A combination of fillet radius and die affects can lead to more desirable outcomes in terms of wrinkle formation and thickness uniformity.
更多查看译文
AI 理解论文
溯源树
样例
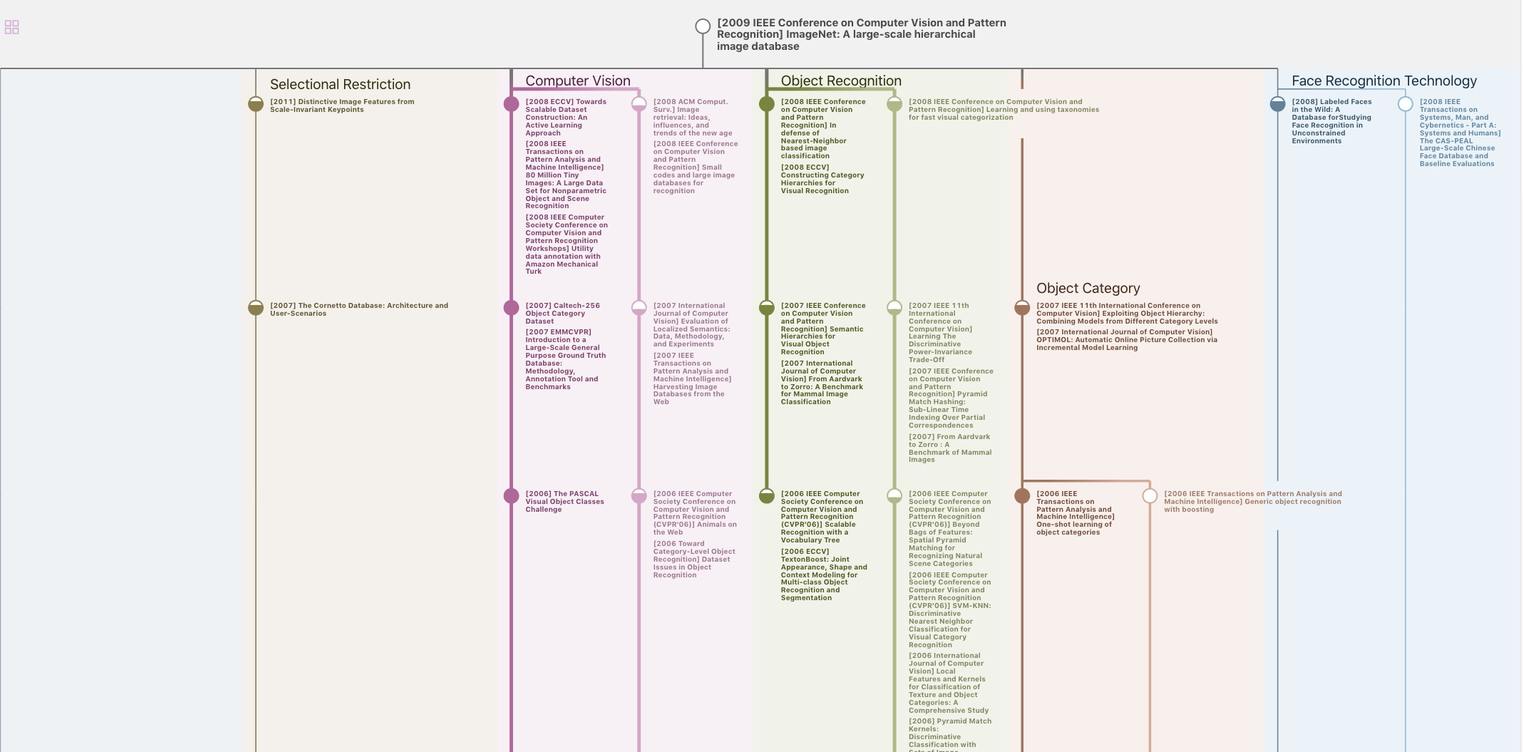
生成溯源树,研究论文发展脉络
Chat Paper
正在生成论文摘要