High-Precision Visual Servoing for the Neutron Diffractometer STRESS-SPEC at MLZ.
Sensors (Basel, Switzerland)(2024)
摘要
With neutron diffraction, the local stress and texture of metallic components can be analyzed non-destructively. For both, highly accurate positioning of the sample is essential, requiring the measurement at the same sample location from different directions. Current sample-positioning systems in neutron diffraction instruments combine XYZ tables and Eulerian cradles to enable the accurate six-degree-of-freedom (6DoF) handling of samples. However, these systems are not flexible enough. The choice of the rotation center and their range of motion are limited. Industrial six-axis robots have the necessary flexibility, but they lack the required absolute accuracy. This paper proposes a visual servoing system consisting of an industrial six-axis robot enhanced with a high-precision multi-camera tracking system. Its goal is to achieve an absolute positioning accuracy of better than 50μm. A digital twin integrates various data sources from the instrument and the sample in order to enable a fully automatic measurement procedure. This system is also highly relevant for other kinds of processes that require the accurate and flexible handling of objects and tools, e.g., robotic surgery or industrial printing on 3D surfaces.
更多查看译文
关键词
neutron diffraction,computer vision,robotics,high accuracy,residual stress analysis,visual servoing
AI 理解论文
溯源树
样例
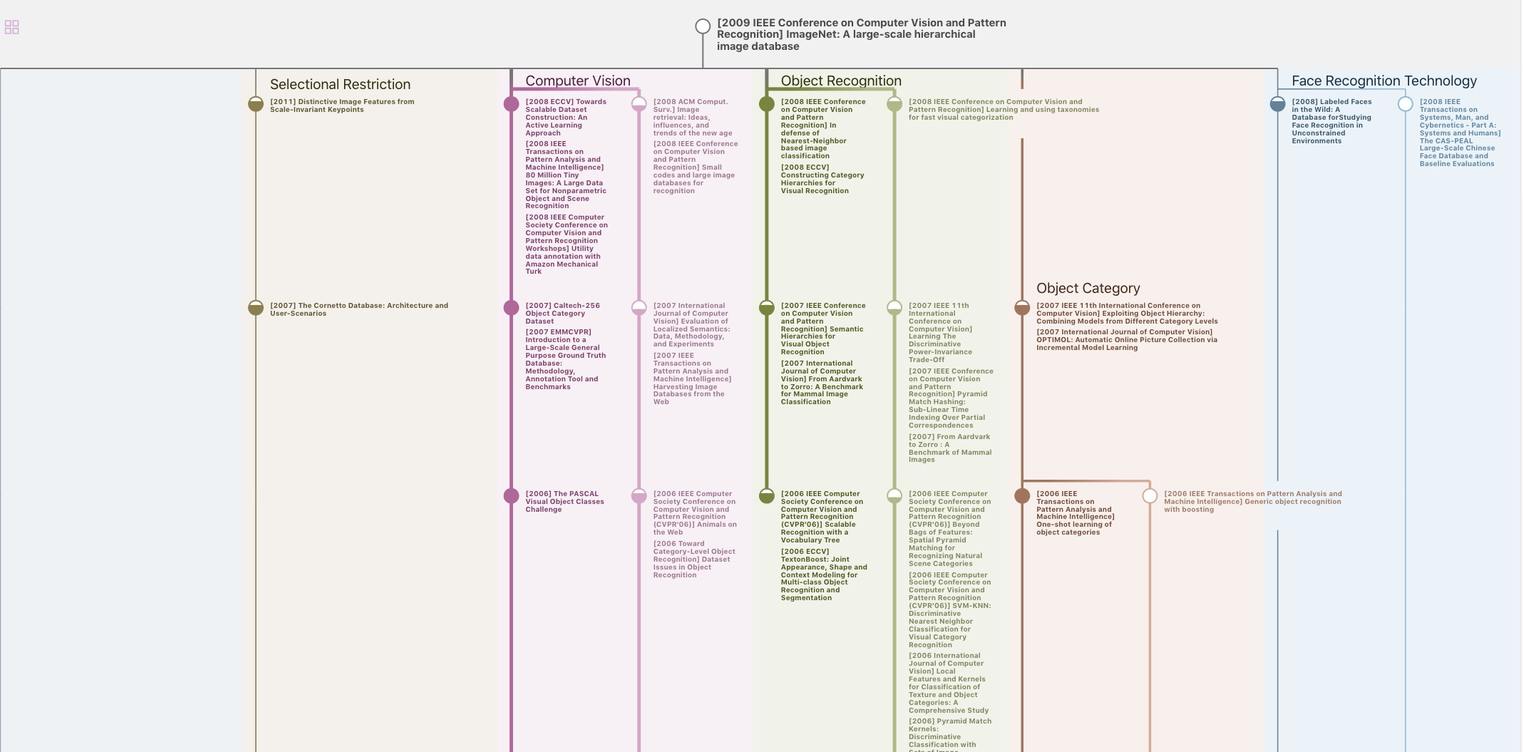
生成溯源树,研究论文发展脉络
Chat Paper
正在生成论文摘要