Optimization Design of Main Hinge Joint Structure Based on Weld Failure Analysis
Engineering failure analysis(2024)
摘要
From the data, structural defects and cracks evolution patterns are identified to determine a statistically significant service life of approximately 5500 h. In this paper, a statistical analysis of failure form and work time of MHJ is conducted. Microscopic test of cracks reveals four main forms of type of cracks. Improper weld technology causes defects in the metallographic structure of weld seam. Improper design causes fatigue cracks of weld seam. Improper machining of parts causes stress concentration and cracks. Improper structural design causes uneven load-bearing capacity of the overall weld structure. According to the above problems, weld structure are optimized. Detailed research is conducted on weld technology of key weld bead. The differences in microstructure and weld efficiency of three different weld technologies are determined by microscopic tests on three key weld seam structures. Therefore, it is concluded that weld bead of MHJ can use full fusion of 9–12 passes multi-pass weld form. This method can achieve a balance between weld efficiency and weld quality. According to simulation analysis and comparison, lifespan after optimization of MHJ increases from 5863 h to 10374.8 h. Structural performance of MHJ is greatly improved after optimization. Effectiveness of optimal design is verified by zero feedback within 5 years.
更多查看译文
关键词
Rotary drilling rig,Weld failure of main hinge joint,Weld structure optimization,Crack of weld seam,Cause analysis
AI 理解论文
溯源树
样例
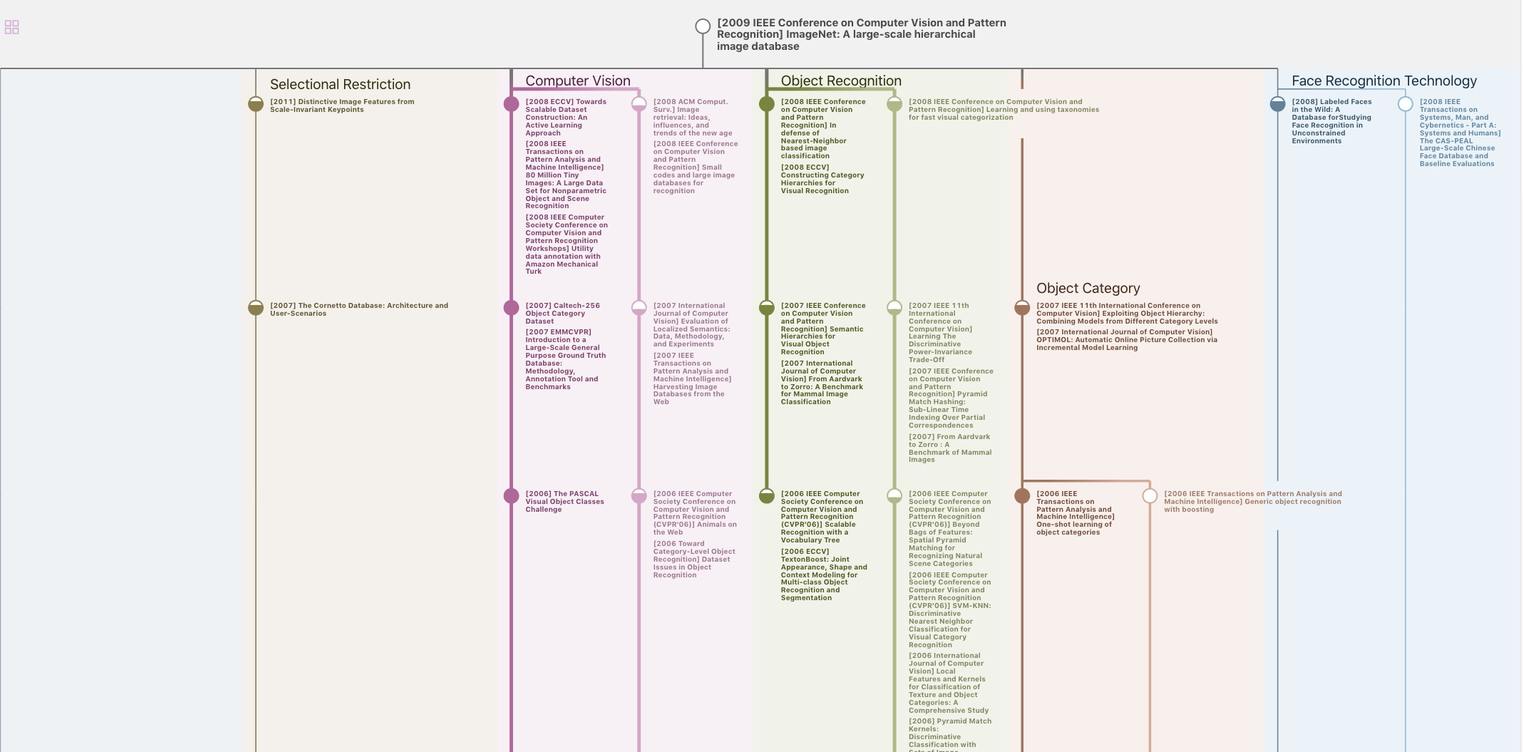
生成溯源树,研究论文发展脉络
Chat Paper
正在生成论文摘要