3D filling simulation of micro- and nanostructures in comparison to iso- and variothermal injection moulding trials
JOURNAL OF MICROMECHANICS AND MICROENGINEERING(2016)
摘要
Flow simulations can cut down both costs and time for the development of injection moulded polymer parts with functional surfaces used in life science and optical applications. We simulated the polymer melt flow into 3D micro- and nanostructures with Moldflow and Comsol and compared the results to real iso- and variothermal injection moulding trials below, at and above the transition temperature of the polymer. By adjusting the heat transfer coefficient and the transition temperature in the simulation it was possible to achieve good correlation with experimental findings at different processing conditions (mould temperature, injection velocity) for two polymers, namely polymethylmethacrylate and amorphous polyamide. The macroscopic model can be scaled down in volume and number of elements to save computational time for microstructure simulation and to enable first and foremost the nanostructure simulation, as long as local boundary conditions such as flow front speed are transferred correctly. The heat transfer boundary condition used in Moldflow was further evaluated in Comsol. Results showed that the heat transfer coefficient needs to be increased compared to macroscopic moulding in order to represent interfacial polymer/mould effects correctly. The transition temperature is most important in the packing phase for variothermal injection moulding.
更多查看译文
关键词
heat transfer coefficient,no-flow temperature,Moldflow,Comsol,transition temperature,life science,optical applications
AI 理解论文
溯源树
样例
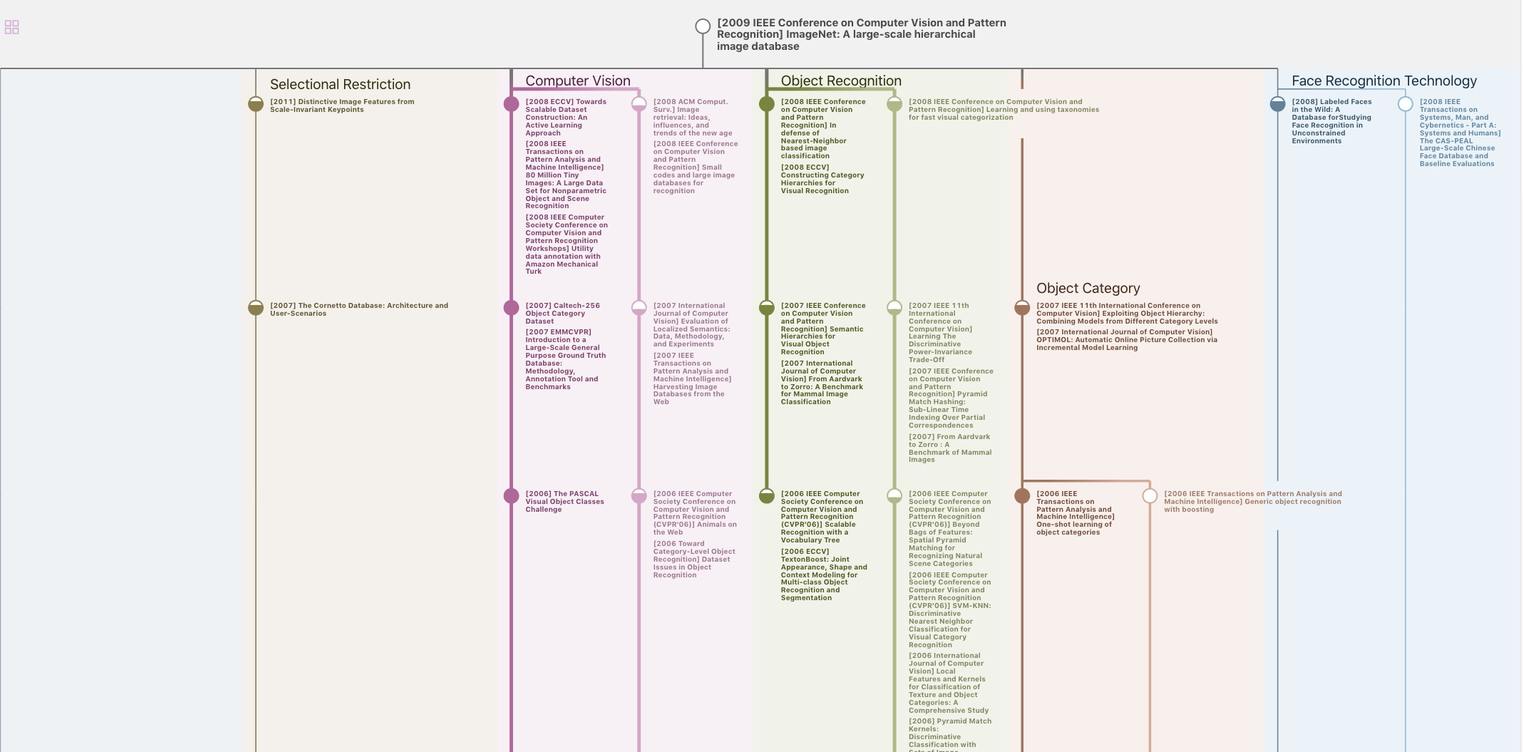
生成溯源树,研究论文发展脉络
Chat Paper
正在生成论文摘要